顧客名
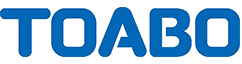
東亜紡織株式会社 宮崎工場様
概要
工場の生産活動に付随する手作業による記録プロセスをIoT機器を活用することで自動化およびデジタル化(デジタイゼーション)しました。
昨今、人材不足の解消や作業効率化などの課題解決にIoTを利用していただく機会が増えました。当社でもIoTを活用しビジネス上の課題を解決しておられるお客様が多くいらっしゃいます。
そんな中、東亜紡織株式会社 宮崎工場様には工場内の電力デマンド、環境データを可視化するため、昨年MORAT GWとEnOceanセンサを導入していただきました。この度、無線接続のMORAT GWを用いて生産量を自動取得し「いつ・何を・どれだけ」作ったのか自動記録する仕組みを提供いたしました。
オンラインセミナー事例紹介
2021年9月8日に開催したオンラインセミナーで当事例をご紹介いたしました。ぜひご覧ください。
アーキテクチャ
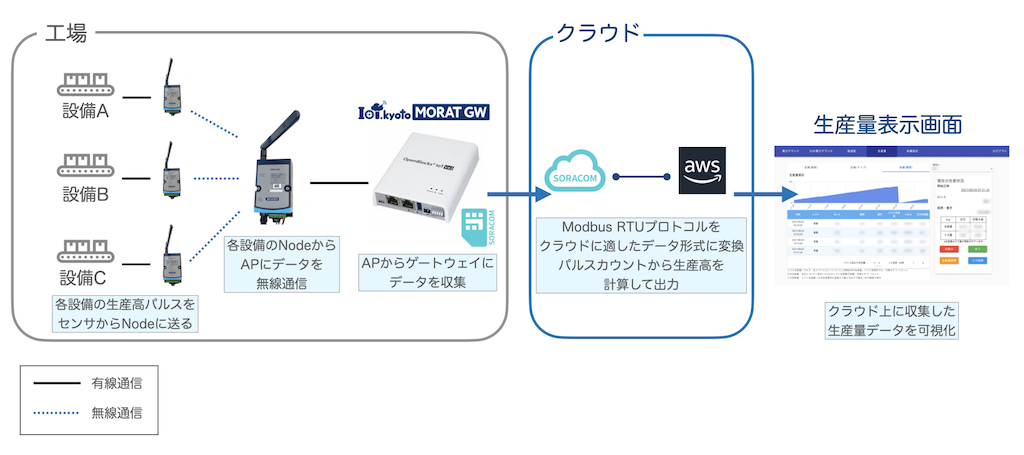
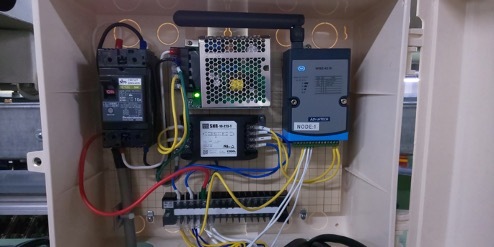
開発経緯
従来より現場の方が創意工夫され、リードスイッチによる回転計と電卓を組み合わせた簡易生産量計により生産量を記録されていました(動画参照)。しかし、電卓の数字は適切なタイミングで紙に転記する必要があり、生産品目により電卓へ入力する係数を変更する必要があるなど、多くの設備を少人数で監視されている中で大きな作業負荷となっていました。
今回は34台の設備からの回転情報(パルス信号)を6台の無線ノードで受け無線APに集約、MORAT GWでクラウドにデータを送る構成としました。配線フリーである無線機器の採用により設置しやすく、障害物や機械ノイズに強い920MHz帯無線もあいまって、工場に設置するのにぴったりだとご評価いただきました。コロナ禍ということもあり、一度も現場に訪問できなかったのですが、工場スタッフの皆さんの手で設置していただき、機器発送後わずか1週間程度でデータを収集、画面に可視化するに至るという、スピード導入を達成しました。
集まったデータは単なる機械の回転数であるため、iPadで生産品目や係数、くず量などを入力し、クラウドで計算処理を行うことで正確に「いつ・何を・どれだけ」作ったかを記録・表示できる仕組みを開発しました。
今回の導入により現場がどう変わったか、トーア紡コーポレーションの中井様と東亜紡織株式会社 宮崎工場の麻生様、中野様にインタビューさせていただきました。
従来のやり方ではダメだという意識があった
—— 今回、生産量パルスを可視化しようと思われたきっかけはありますか?
製造業の国内生産は年々多品種小ロット化しています。確保できる人材も減少しており、生産量が減少していても作業者の負担が増大しています。これは生産に多大な影響があるのではないかと考えています。
元々は動画の通り、電卓を使って計算した数字を目視と手書きで集計していました。しかし過去、管理者がやっていたことを現在は一般社員がやらなければなりません。ある程度省力化は進んでいますが、それ以上に人が減っています。従来のやり方ではダメだという意識がありました。そこで生産の集計作業を自動化し、見える化によって生産状況を把握することで、「目視と手書きの集計を行う」という作業がなくなり、他の作業を行うことができ、作業効率を上げ課題が解決できると考えました。
また、手書きでの集計はどうしても走り書きになってしまい、あとから読み返すことが難しかったり、間違えてしまうリスクがありました。これを自動化することで、間違うことがなくなります。既存のプロセスをデジタルに変化させるデジタイゼーションを行うことで人材不足、業務効率化をはかります。
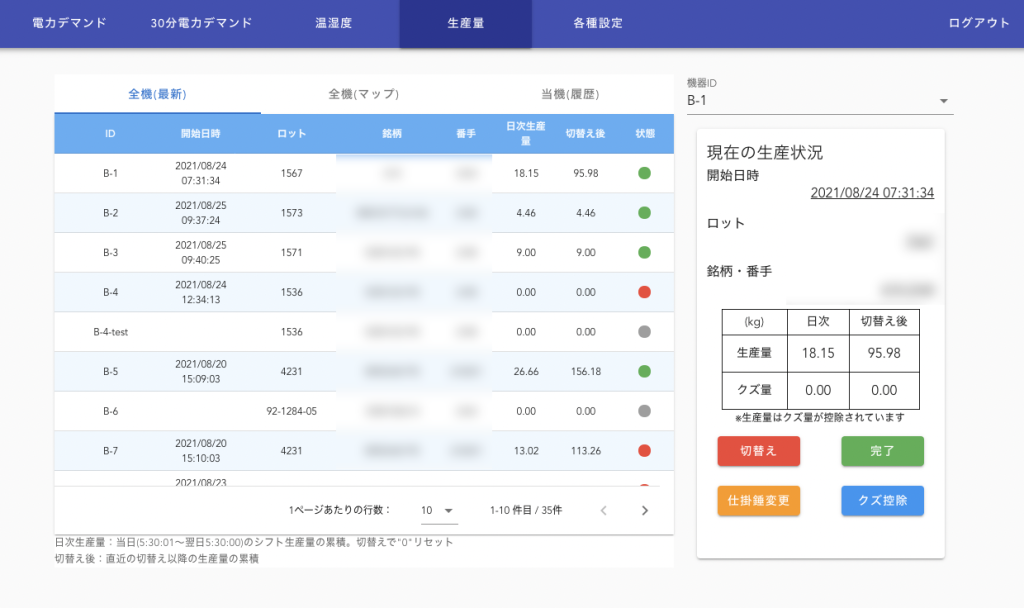
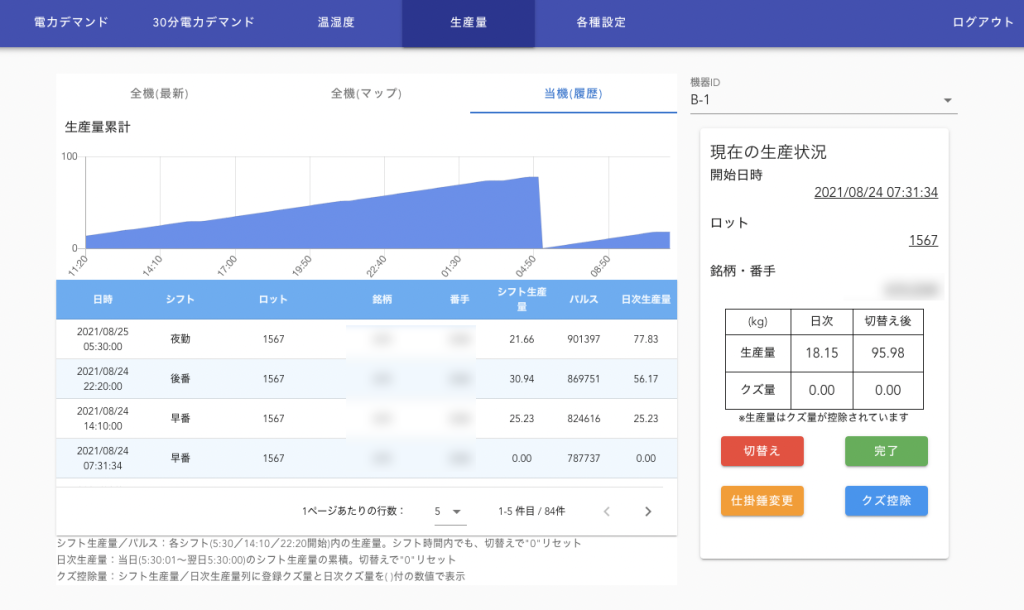

何事もやってみないとわからない
—— 導入後の現場の様子の変化や作業員の皆様の反応は何かありましたか?
IoT化という言葉を耳にする機会が多くはなりましたが、日常生活でIoTに意識を向ける方が多いわけではありません。残念ながら今回の生産高パルスのIoT化については戸惑いや不安の声が大きいです。実際に使用してみていますが、切り替えや入力がちょっと難しいかもしれません。まだ導入直後なので、改善点は突然集計がIoT化したため、ルールなどはこれから決めていくところです。ただ、今回の導入をしたことで、今まで考えていなかったことを考えだしていると感じています。
これまでも作業の効率化については様々な工夫をしながら変化してきた歴史があります。これからも現場の皆さんが自ら考えることで、効率化を進めていけるのではないかと期待しています。今回の生産高パルス可視化システムの導入は効率化のきっかけに他なりません。もしかしたら必ずしも現地にいなくてもいいかもしれないという意識が生まれ、管理する事務系の人材を県外から求人できるかもしれません。業務を最適化するまではまだまだ道半ばです。データを可視化したら何かがすぐ変わるとも思いません。ただ、作業者の負担が増大していることは間違いありませんし、変わらざるを得ません。何事もやってみないとわからないことだらけです。
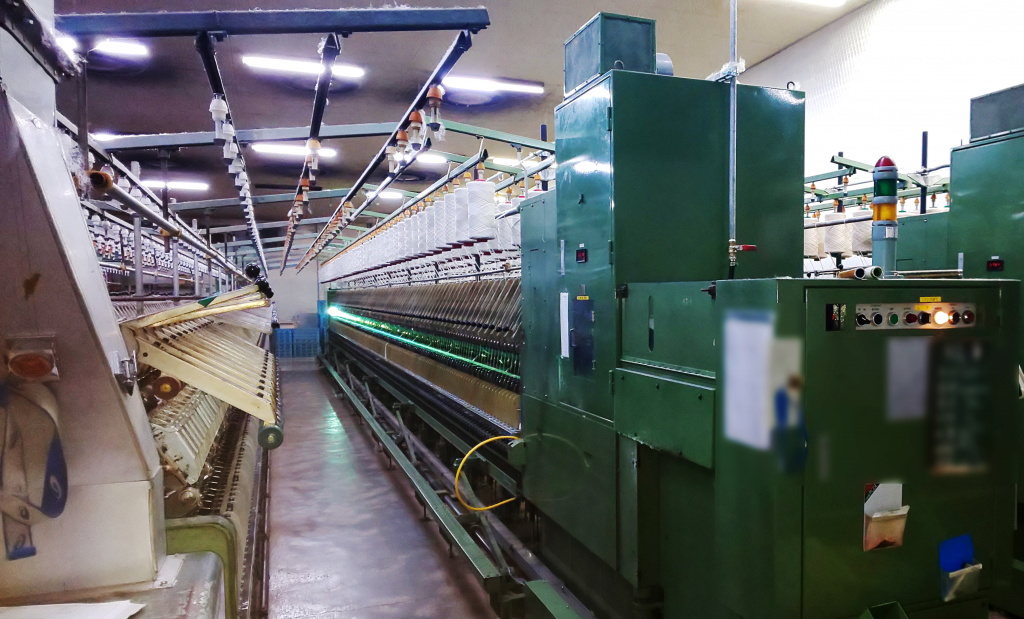
—— 今後の展開やIoT.kyotoに期待していることはありますか?
製造工程で課題を出しつつ、業務の改善を進めていきます。今後も新たな提案や課題も出てくるので、他の工程でも横展開してスマートファクトリーを目指します。
全国的にDX化という言葉が一人歩きしていますが、IoTは単なるきっかけです。今回の導入現場の方々、管理者の方々の考え方が変わっていくことを期待しています。業務改善や業務改革ができたら幸いです。IoTは導入したら終わりではありません。導入してどう変化していくかが勝負です。このIoT導入を通して、生産・品質にまで影響が出てくれたらうれしいですね。それから、これをきっかけに現場の方々のモチベーションが上がり、より効率化を意識して取り組んでいけるように今後もIoT化を進めていきたいと考えています。
まとめ
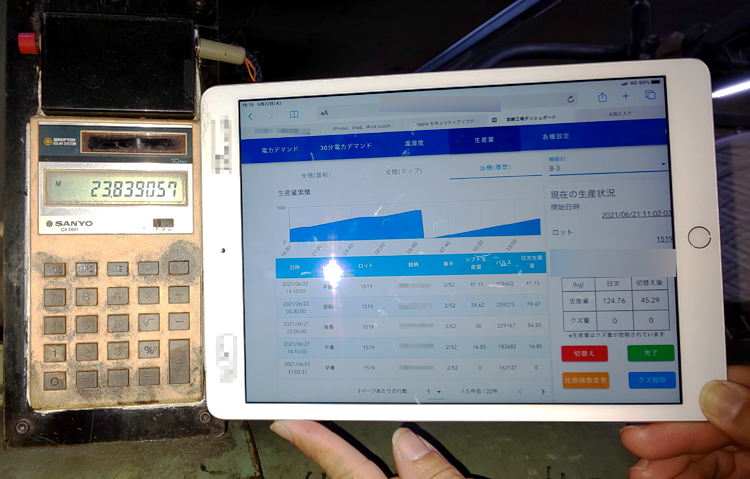
電卓で目視、手書きしていたデータが現在はiPad上でグラフ、一覧で可視化できるようになりました。新旧のデータ確認方法を並べた画像をいただいたので掲載いたします。実際に目にするとかなり大きな変化だと感じられるのではないでしょうか。変化には戸惑いや不安はつきものです。これからこの導入をきっかけに業務改善に進むとのことで、今後の展開を私たちも楽しみにしています。
今回のインタビューで「IoTは単なるきっかけ、道具でしかない」とお話していただきました。IoT.kyotoではこのきっかけを提供し、お客様自身の課題解決にご協力をしています。IoT.kyotoにも保守体制がありますので、導入して完了にはなりません。ご不明点や改善点があれば、ご相談していただき、お客様の課題解決まで伴走いたします。
-
Modbus RTU対応機器で手軽にセンシング&コントロール